The History of Oil Filtration
Motor oil filters have come a long way since the first design was introduced in the 1920s.
One of the most important functions of motor oil is to capture and suspend contaminants and wear particles,
preventing premature wear on an engines internal parts. Acting alone, motor oil would quickly become saturated
with these contaminants and wear materials and would require very frequent changing, perhaps as often as every 500
miles, in order to effectively guard against wear. It is an engines oil filter which allows motor oil to last for
an extended period of time.
The earliest automobiles did not have any sort of oil filtration, and it was common to change oil every 500 to 2,000 miles. Later, as pressure lubrication became standard on automobiles, some kind of oil filtration was necessary in order to protect the oil pump from damage and wear. Early designs were quite primitive, often consisting of nothing more than steel wool, wire meshes or screens placed in the oil pump intake. Many designs were cleanable and reusable.
The earliest incarnation of the modern oil filter came about in 1923, when Ernest Sweetland introduced his
invention known as the Purolator, a combination of the words Pure Oil Later. Incorporated into the lubricating
system after the oil pump and before the oil flows into the engine bearings, the original Purolator featured an
upright series of seven twill weave cloth-covered, perforated plates encased in a heavy-duty cast container. It
also had a sight feed glass on one side, enabling the owner to see the oil flow and change the filter when flow
slowed to a trickle.
James A. Abeles saw enough potential in the Purolator to convert a New York City garage into a company called Motor Improvements Inc., developed primarily to manufacture Purolator filters. The Maxwell Chalmers Company also saw promise in this new product, installing a Purolator on a Maxwell automobile which was test-driven on a round-trip from Detroit to the West Coast in 1924. The longer oil drain intervals, cleaner oil and reduced engine wear offered by the Purolator ensured endorsement by the automotive industry, and they soon became standard on many popular automobiles of the day, including Studebaker, Pierce Arrow, Hupmobile, Peerless, Cadillac, Oakland, Gardner, Moon, Jordan, Buick and Dodge.
Oil filter technology continued to progress over the years. In the late 1930s, cotton waste material was
introduced as filtration media, providing the first filter replacement capability. Various woven fabrics were
also used in some filter designs. By 1946, as disposable filter models became the norm and interest in saving
production costs increased, materials such as pleated paper and cellulose became the filtration media materials
of choice, materials that are still widely used in todays oil filters.
Prior to 1943, most oil filters were of the by-pass variety, only filtering about 10 percent of the oil at a time. The first full-flow oil filter, capable of filtering 100 percent of the motor oil, was introduced in 1943 and became standard on mass production vehicles by 1946.
The modern disposable "spin-on" oil filter design was introduced in 1955, replacing cartridge-type filters
which had to be placed in a special housing or canister. The technology progressed throughout the 1960s and
spin-on oil filters soon became standard on virtually all American, European and Japanese automobile designs.
Todays spin-on oil filters resemble metal cans that encase the filtration media, which capture and hold the various organic and inorganic contaminants and wear metals within the motor oil. Organic contaminants include bacteria and other organisms that make up sludge, while inorganic contaminants include dust and dirt.
An engines oil pump pumps motor oil from the oil sump to the oil filter. Dirty oil passes through the oil filter media, where it is cleaned before flowing to the central tube and back into the engine through the mounting stud. Oil is then distributed by oil passages throughout the engine.
Secondary by-pass oil filters act separately from an engines full-flow filter and only filter a small portion of the oil in a system at a time, subjecting it to additional and more thorough cleaning than the full-flow filter is able to provide.
Various styles of by-pass systems exist on the market today. Some feature centrifuge or thermal action, spinning or boiling out contaminants, while others feature extremely efficient media that remove smaller contaminants. Originally marketed as a way to effectively extend equipment life, the use of by-pass filters are also effective in keeping oil clean and capable of extended drain intervals.
The AMSOIL Advantage
As previously mentioned, many of todays conventional oil filters make use of pleated paper or cellulose as their filtration media. Although these filters usually display good flow characteristics when new, they tend to become obstructed fairly quickly. In addition, these conventional filters exhibit limited capacity, longevity and ability to catch fine particles.
AMSOIL Ea (Absolute Efficiency) Oil Filters are designed for maximum efficiency, capacity and longevity, while meeting the high flow demands of modern engine designs. In fact, with its advanced filtration media composed of a special synthetic nanofiber, AMSOIL Ea Oil Oil Filters have over a 100 percent better combined efficiency/capacity rating than other popular oil filters as tested according to industry standards. AMSOIL Ea Oil Filters are also approximately 98.7 percent efficient at removing 15 micron particles. In addition, AMSOIL Ea Oil Filters are designed for extended drain intervals of 25,000 miles or 1 year (whichever comes first), making them ideal for use in conjunction with premium AMSOIL Synthetic Motor Oils.
AMSOIL By-Pass Filtration
Advanced engine designs place tough demands on an engines full-flow filter, most of which are capable of efficiently filtering out only coarser wear particles, generally greater than 20 to 25 microns. However, approximately 60 percent of engine wear is caused by particles in the 5 to 20 micron range. These tiny particles closely match the precision clearances between critical engine components, entering the spaces between bearings, rings and other components and damaging metal surfaces, altering tolerances, fatiguing components and generating additional debris. For the ultimate in filtration efficiency and wear protection, AMSOIL offers the Spin-On By-Pass Oil Filter.
The AMSOIL By-Pass Oil Filter provides the best possible filtration on the market, protecting against wear,
oil degradation, rust and corrosion. Situated outside the main line of oil circulation, the AMSOIL By-Pass Filter
works in conjunction with the full-flow filter, thoroughly filtering 10 percent of the oil at a time and removing
wear-causing contaminants down to less than one micron in size. The AMSOIL By-Pass Filter effectively filters all
the oil in a six quart system in about five minutes at an average speed of 45 mph.
Water enters motor oil as a combustion by-product or as a condensate. When it contaminates motor oil, it can cause serious engine damage by causing metal surface rust and corrosion, which increases friction and wear and deteriorates the close-fitting tolerances between engine components. It can also react with other contaminants to form corrosive acids, which also damage metal components. The AMSOIL By-Pass Filter effectively removes up to a pint of damaging water, significantly increasing the time oil can be safely left in the engine.
The effectiveness of the AMSOIL By-Pass Filter lies in its construction. Its high-capacity filtration medium is a special blend of virgin wood and cotton fibers, formed into discs, stacked and compressed. The center tube is all-steel, perforated for oil flow and wrapped with a fine mesh cotton screen. Each filter includes a mounting unit with a spin-on filtering cartridge, connected by hoses to engine ports. The entire by-pass system fits into most cramped engine compartments, allowing quick and easy access. Particles sized down to less than one micron are trapped and removed, while the filters thirsty cellulose fibers remove water.
By-Pass Filter Accessories:
The AMSOIL Dual Remote Oil Filtration System allows an AMSOIL Ea Oil Filter and an AMSOIL Spin-On By-Pass Filter to be attached onto a remote mount, providing easy access for both filters. Remote placement of the Dual Remote system allows larger oil filters to be used and increases oil sump capacity.
The AMSOIL Dual-Gard Filtration System links two AMSOIL By-Pass Filter elements together for engines with sump capacities greater than 20 quarts.
We're now on Facebook!
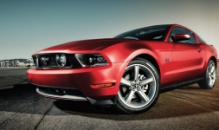
Buy at wholesale price!
Preferred Customers buy at dealer cost and save 25%!
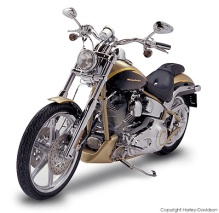
Not sure which products to get for your vehicle? Use the Vehicle Lookup Guide.
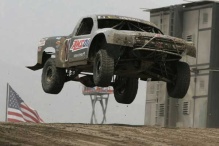
AMSOIL Distributor Opportunities
Start your own home business based on a proven superior product. Very low startup costs.
Sell AMSOIL products in your shop or store. Click here for information on AMSOIL retail accounts.
Does your business purchase lubricants for its equipment? Click for information about AMSOIL commercial accounts! Extend your equipment's life and reduce costs!